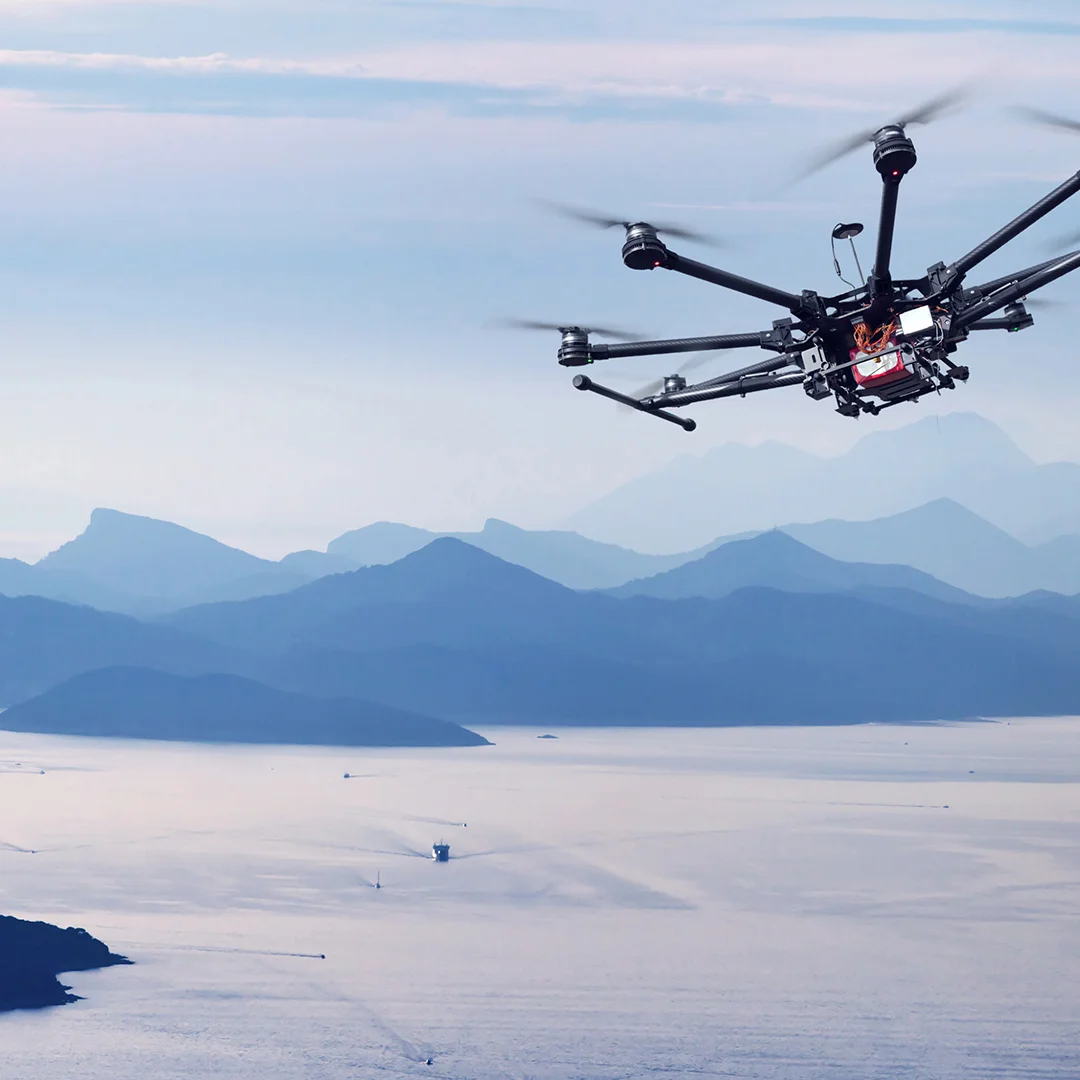
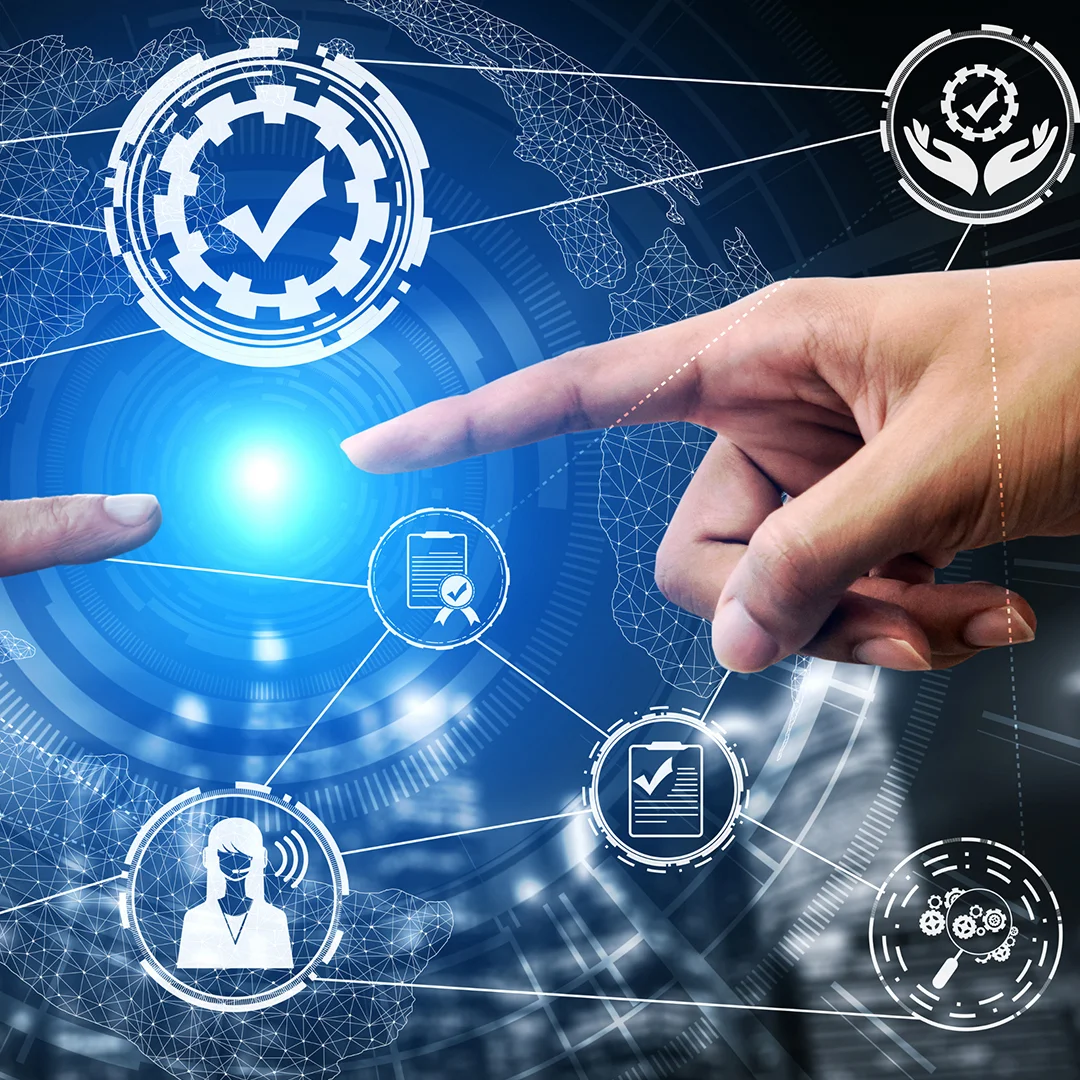
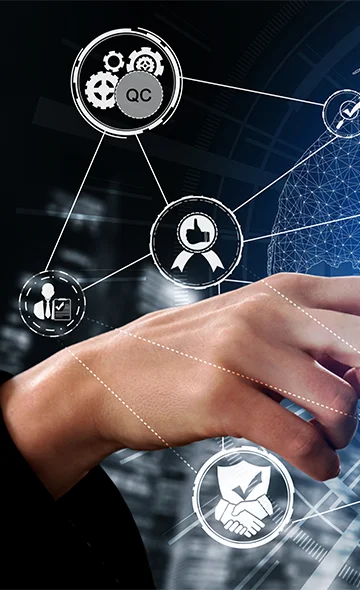
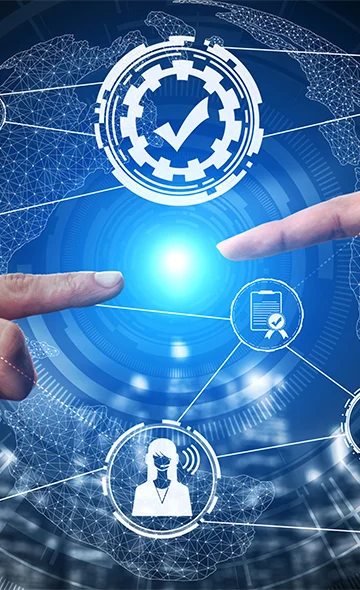
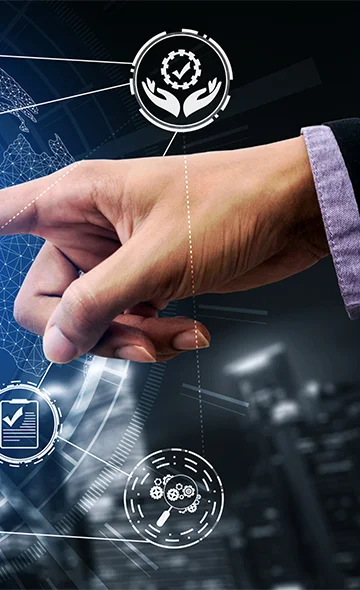
QA/QC SUPERVISION
Preventing the creation of inaccurate or incorrect data is the most effective way to ensure the quality of your products and decisions that rely on that data. QA refers to the use of various criteria, methods, and processes that will ensure that the generated deliverables meet a defined quality standard.
It can be stated with certainty that every measurement is subject to errors, whether caused by human factors or the imperfections of the devices used for the specific measurement. Some errors resulting from physical characteristics are repetitive, meaning they are systematic. For some other errors, this cannot be said, i.e., they are entirely random. Depending on their impact, measurement errors can be divided into systematic and random errors. However, before their more precise determination, it is necessary to define errors often referred to as gross errors or blunders.
Quality control (QC) refers to the application of methods or processes that determine whether generated data meet defined quality criteria and to what extent our results contain errors. Digital Dome has developed various mathematical models, automatic and semi-automatic procedures and manual processes over time to detect errors. By understanding the nature of errors and the laws of their impact, some errors can be reduced or completely eliminated.
QA/QC SUPERVISION
QA/QC (Quality Assurance/Quality Control) is essential for ensuring the quality of products and services in any company. Here are some key benefits of QA/QC:
- Improved customer satisfaction
- Reduced costs
- Improved efficiency
- Enhanced reputation
- Compliance
- Continuous improvement
Every company should have a QA/QC program in place to ensure that their products and services meet the highest quality standards and to maintain customer satisfaction and loyalty.
General Services
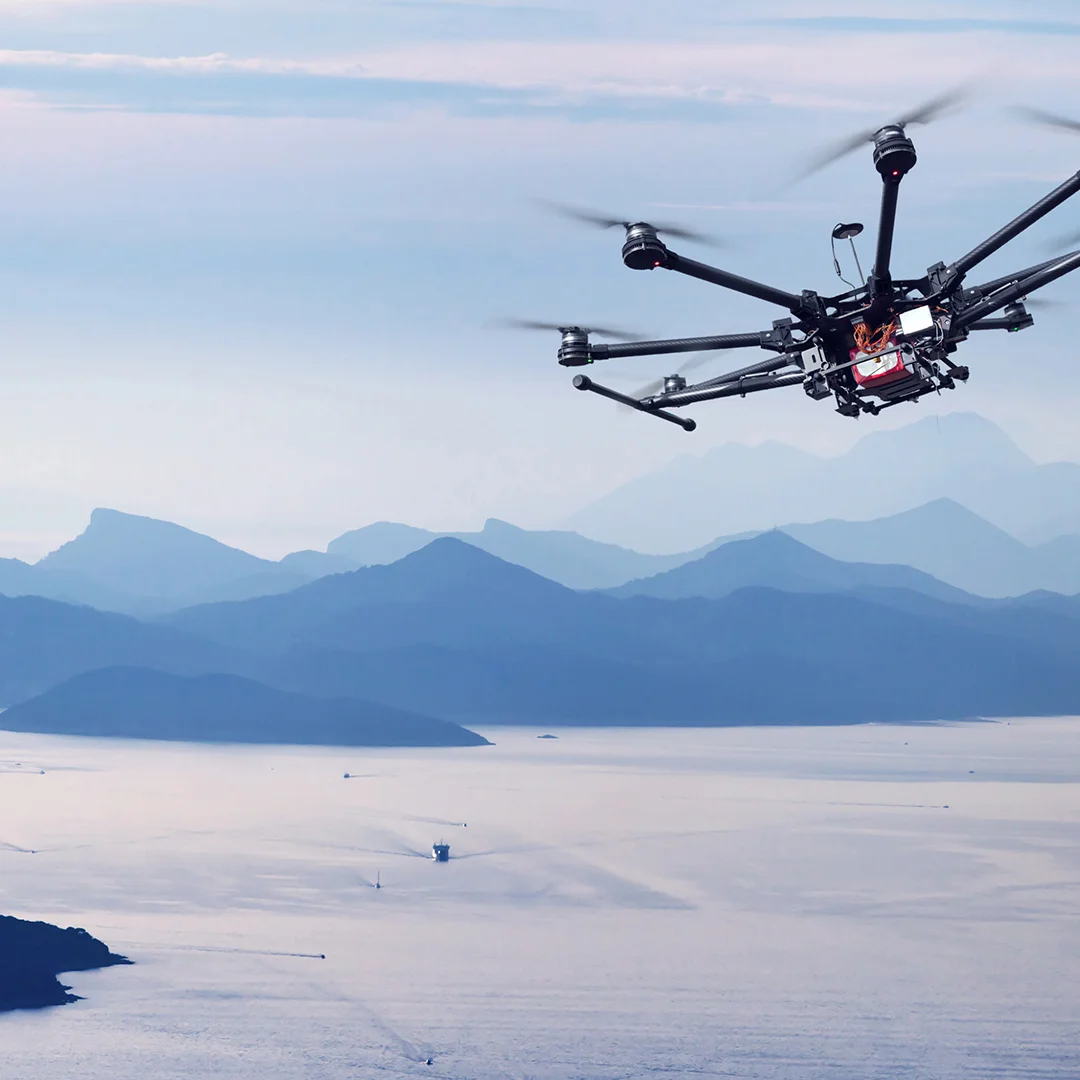
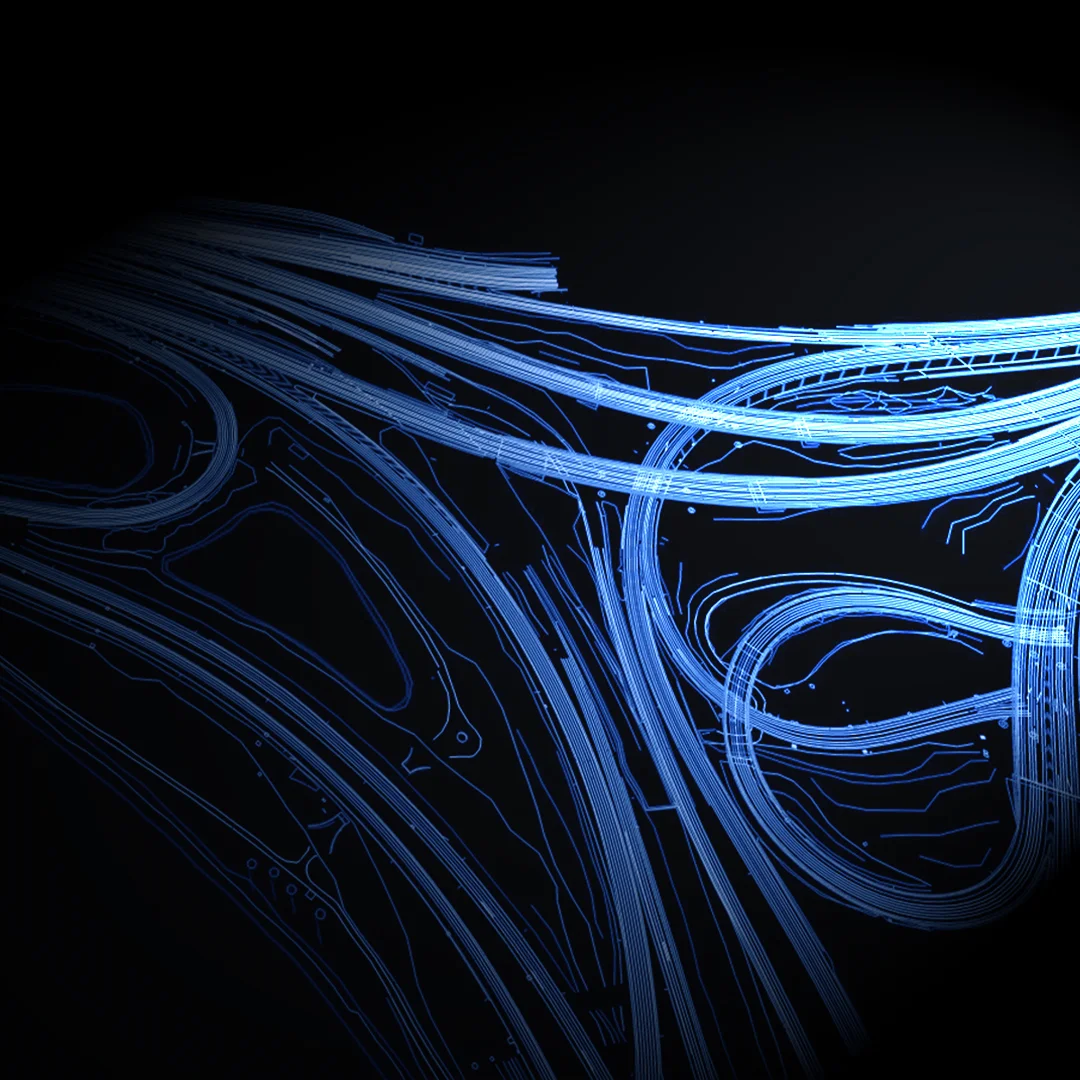
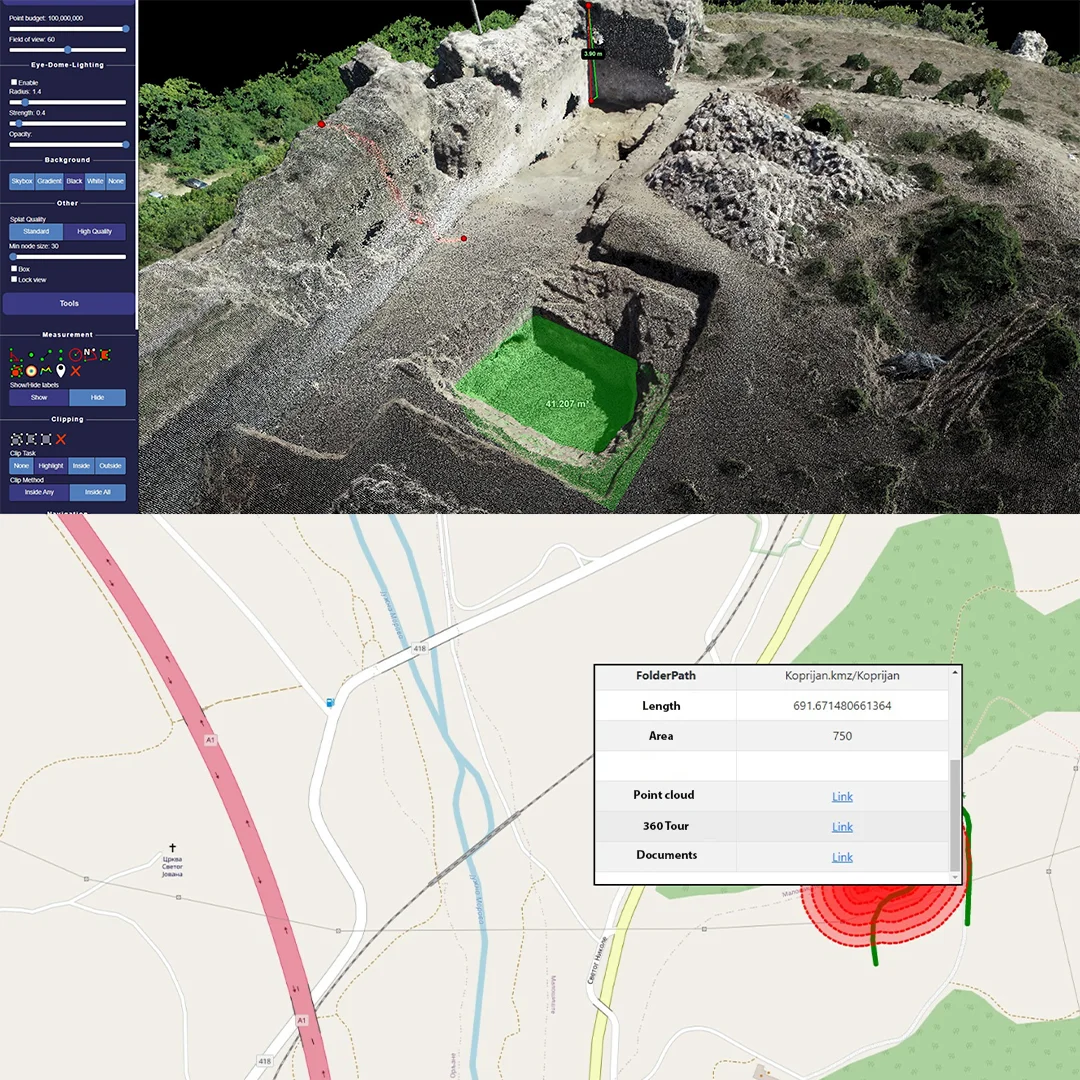
DEVELOPMENT OF PORTALS AND ON-LINE SERVICES FOR SPATIAL INFORMATION MANAGEMENT
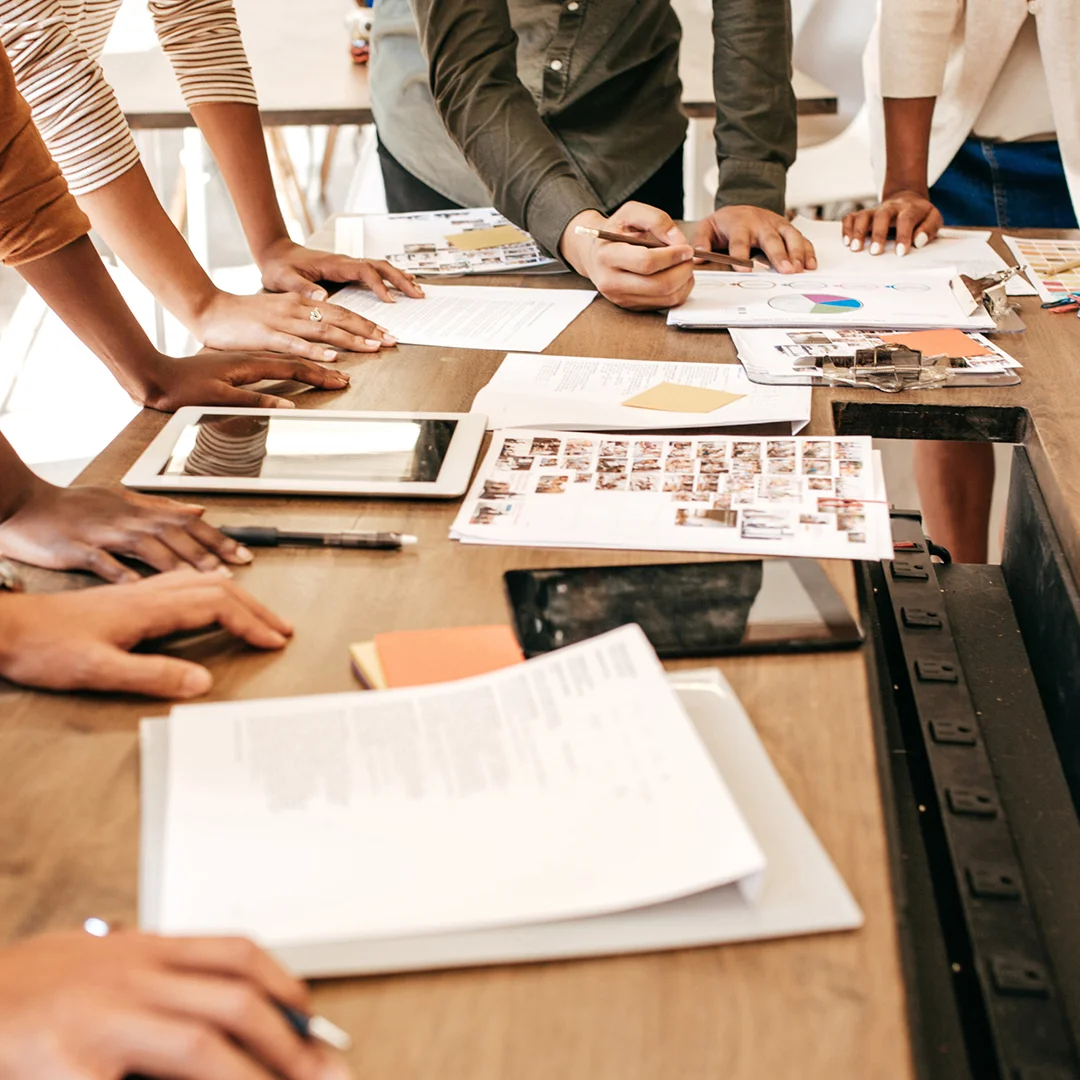